The Ultimate Guide to Plastic Mold Tools: Enhancing Manufacturing Efficiency
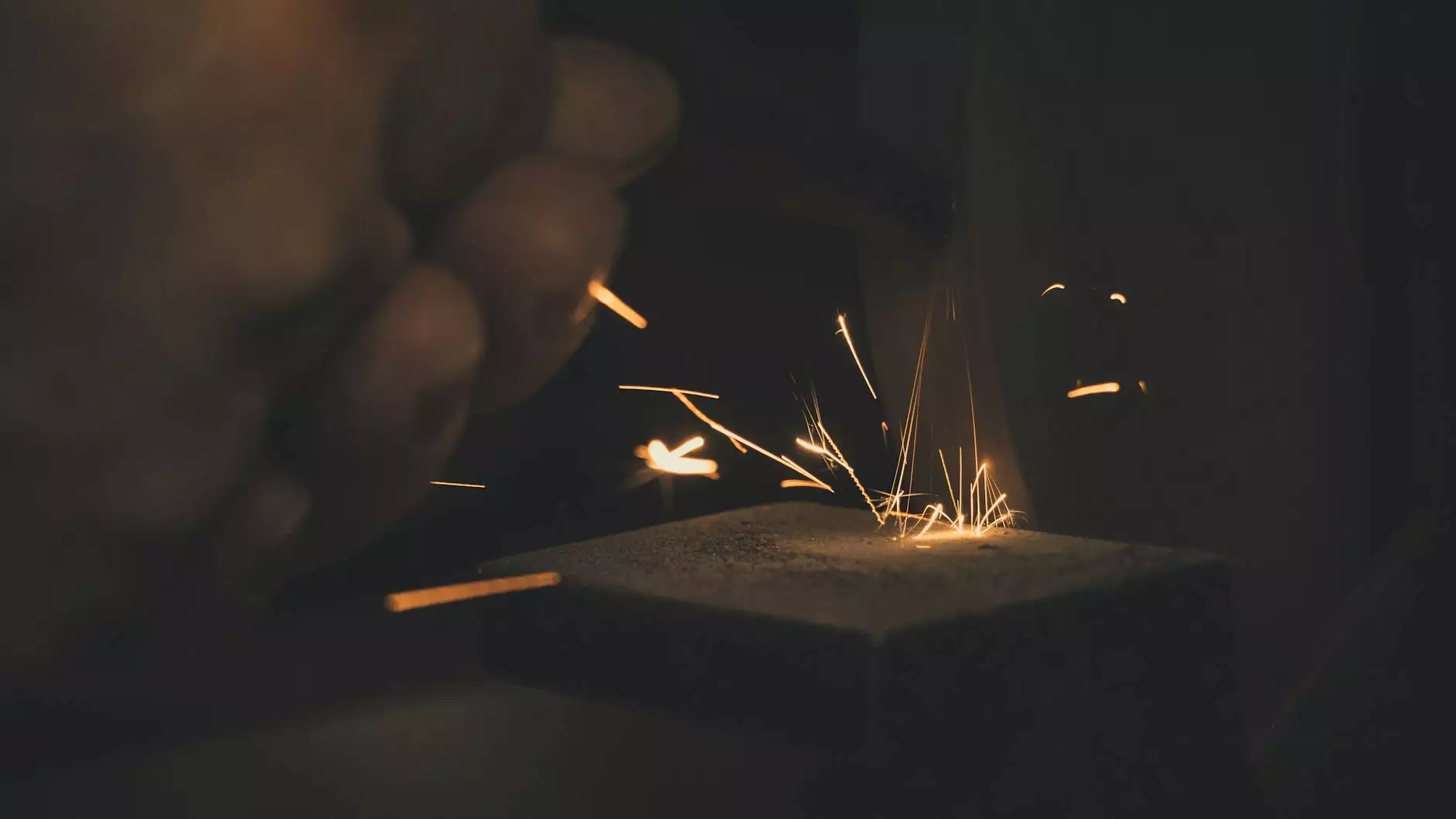
In the fast-evolving world of manufacturing, plastic mold tools have emerged as an indispensable component for efficient production processes. This article explores the pivotal role these tools play in the metal fabricators industry, how they enhance operational efficiency, and their contribution to sustainability.
Understanding Plastic Mold Tools
Plastic mold tools are precision-engineered instruments used in the molding process, particularly in the creation of plastic parts. They facilitate the transformation of raw plastic material into a variety of durable and intricately designed components. The use of plastic mold tools significantly streamlines production workflows and ensures high-quality outputs, making them essential for businesses aiming to remain competitive in today's market.
Types of Plastic Mold Tools
There are several types of plastic mold tools utilized in manufacturing, including:
- Injection Molds: These are among the most common types of molds where plastic is injected into a mold cavity to form a specific shape.
- Blow Molds: Often used for hollow objects like bottles, blow molds use air pressure to expand heated plastic into a mold.
- Compression Molds: This molding involves placing plastic in a heated mold cavity where it is compressed by a heated platen.
- Rotational Molds: Relevant for large hollow parts, rotational molds allow the material to coat the interior surfaces of a mold while it is rotated.
The Significance of Plastic Mold Tools in Manufacturing
The significance of plastic mold tools in manufacturing cannot be overstated. They directly impact production rates, cost efficiency, and product quality. Here’s how:
1. Enhanced Production Efficiency
With the automation of injection molding processes, plastic mold tools enable high-speed production of components. This means that manufacturers can produce larger quantities in shorter times, ultimately enhancing productivity.
2. Precision and Consistency
Plastic mold tools are designed with tight tolerances, ensuring that each item produced meets the specified standards for accuracy and quality. This precision is crucial for industries such as automotive and medical devices, where even minor discrepancies can lead to significant failures.
3. Cost-Effective Production
While the initial investment in high-quality plastic mold tools may be substantial, the long-term savings in material costs, labor, and waste reduction make them a wise investment. These tools provide the ability to produce parts with minimal scrap, significantly lowering production costs.
4. Versatility in Design
One of the most compelling advantages of using plastic mold tools is their ability to produce complex designs. Modern tools can create intricate geometries that would be impossible or too costly with traditional manufacturing methods.
Sustainability and Environmental Impact
As the world becomes more conscious of sustainability, the role of plastic mold tools in creating environmentally friendly products is increasingly relevant. By optimizing material use and minimizing waste, manufacturers can contribute to a circular economy.
Reduced Waste with Smart Design
Thoughtful design and engineering of plastic mold tools can significantly reduce material waste. The design process involves considering how to achieve maximum efficiency, which often includes recycling scrap material back into production.
Innovative Materials
Additionally, advances in material science have led to the development of sustainable plastics, such as bio-based resins, which can be used in conjunction with modern plastic mold tools. This synergy promotes the manufacturing of eco-friendly products without compromising on performance or quality.
Choosing the Right Plastic Mold Tools for Your Business
Selecting the appropriate plastic mold tools is crucial for any manufacturing operation. Here are key considerations to keep in mind:
1. Understand Your Production Needs
Assess your specific production requirements, including the types of products you manufacture, the volume of production, and any unique design features that your parts must possess. This assessment will guide you in selecting the right tools.
2. Evaluate Quality and Precision
Not all plastic mold tools are created equal. Opt for suppliers with a proven track record of quality and precision. Highly accurate molds lead to fewer defects and rework, saving time and money in the long run.
3. Consider Maintenance and Support
Maintenance is a critical factor in the longevity of plastic mold tools. Choose suppliers who offer strong support services, including maintenance, repairs, and upgrades.
4. Cost vs. Value
While it may be tempting to choose the cheapest option available, consider the value and total cost of ownership. High-quality plastic mold tools may have higher upfront costs but can offer better long-term savings and performance.
The Future of Plastic Mold Tools
As technology advances, the future of plastic mold tools looks promising. Emerging technologies such as 3D printing and smart manufacturing are set to revolutionize the industry. Here are some trends to watch:
1. Integration of 3D Printing
The integration of 3D printing into the production of mold tooling offers significant advantages, including rapid prototyping and the ability to create complex designs that are cost-prohibitive with traditional methods.
2. Smart Manufacturing and Automation
The rise of the Internet of Things (IoT) and smart manufacturing tools mean that manufacturers can obtain real-time data from their plastic mold tools, enhancing operational efficiency and predictive maintenance capabilities.
3. Global Market Expansion
As industries around the globe continue to expand, the demand for sophisticated plastic mold tools will rise. This trend creates a wealth of opportunities for businesses like Deep Mould that specialize in high-quality tooling solutions.
Conclusion: Investing in Plastic Mold Tools for Future Success
In conclusion, plastic mold tools are fundamental to the success of modern manufacturing operations. Their ability to enhance production efficiency, ensure quality, and support sustainability makes them invaluable. As technology continues to evolve, businesses must invest in high-quality mold tools to remain competitive, reduce costs, and meet the changing demands of the market.
By choosing the right plastic mold tools, you not only improve your manufacturing process but also position your business for long-term success in an increasingly complex and challenging landscape. Embrace the future of manufacturing—invest in plastic mold tools.