Understanding Precision CNC Machining Factories: A Comprehensive Guide
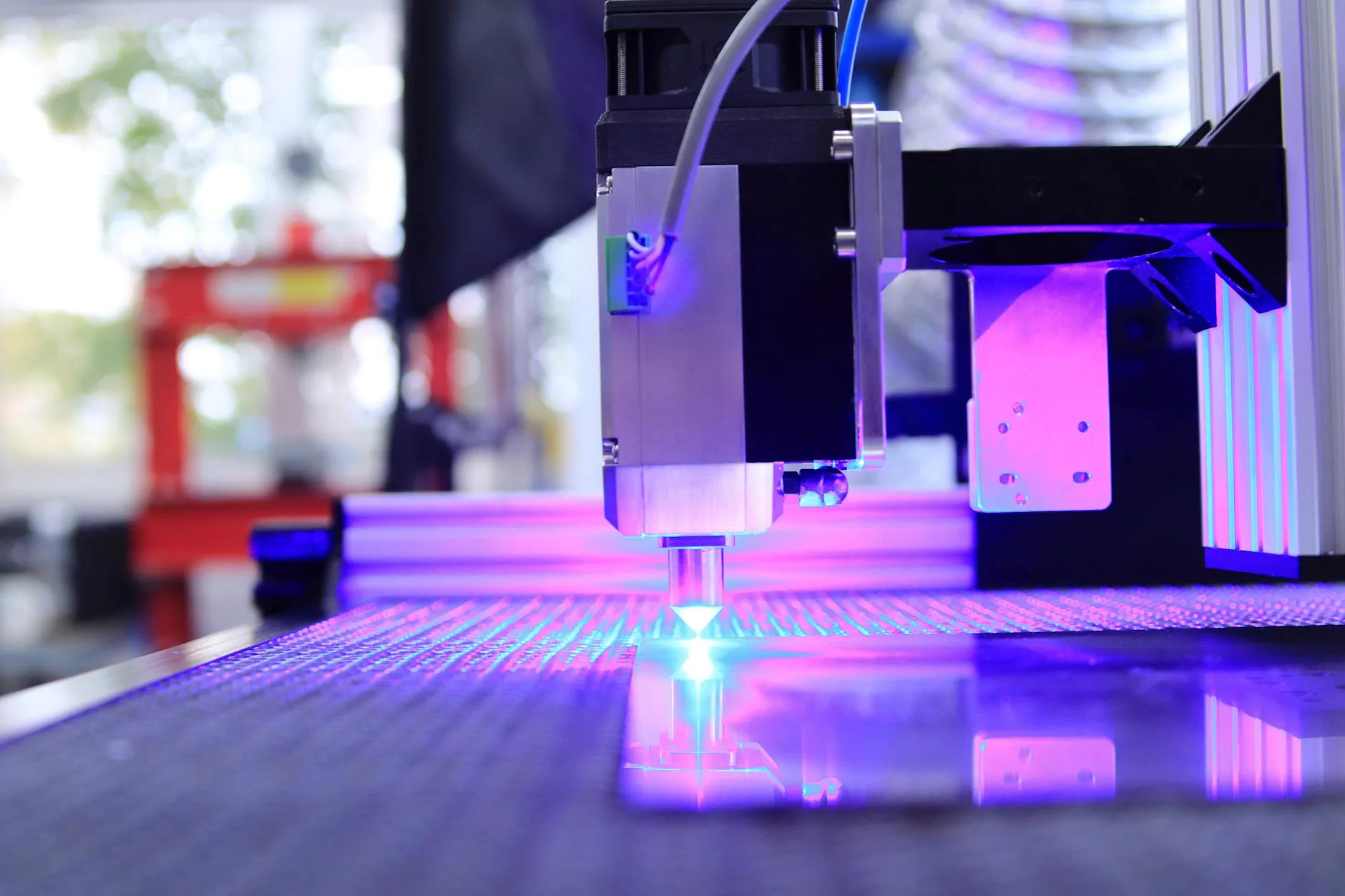
In today’s rapidly evolving manufacturing landscape, precision CNC machining stands out as a hallmark of innovation and efficiency. As businesses strive to enhance productivity and quality, precision CNC machining factories play a pivotal role in crafting intricate components with unparalleled accuracy. This article delves deeply into the functionalities, technologies, and benefits of these factories, providing insights that can help manufacturers and consumers alike.
The Essence of Precision CNC Machining
CNC machining, short for Computer Numerical Control machining, involves the automated control of machining tools via a computer. It is a manufacturing process that utilizes pre-programmed computer software to dictate the movement of machinery and tools. This technology allows manufacturers to create extremely precise and complex parts across various materials, primarily metals. The degree of precision offered by CNC machining has made it a cornerstone in industries such as aerospace, automotive, medical devices, and more.
The Role of Precision CNC Machining Factories
Precision CNC machining factories are specialized facilities equipped with advanced CNC machines that produce high-quality components. They serve a multitude of industries and fulfill various functions:
- Mass Production: One of the significant advantages of CNC machining is its efficiency in mass production. These factories are capable of producing thousands of identical parts with minimal human intervention.
- Custom Fabrication: CNC machining allows for customization, making it ideal for creating bespoke parts tailored to specific client requirements.
- Prototype Development: Factories provide prototyping services that allow businesses to test designs before moving into full-scale production.
- Complex Geometries: CNC machines can manipulate materials to create complex shapes and intricate designs that would be impossible to achieve through traditional machining methods.
The Technology Behind CNC Machining
The technology behind CNC machining has evolved significantly, allowing for high levels of precision and automation. Let's explore some of the critical technologies that underpin precision CNC machining factories:
1. CNC Machines
CNC machines come in various forms, each suitable for specific tasks:
- CNC Mills: Used for cutting and shaping materials by removing excess material.
- CNC Lathes: Specifically designed for shaping cylindrical objects.
- CNC Routers: Ideal for cutting large sheets of materials.
- CNC Plasma Cutters: Utilized for cutting through metal using plasma technology.
2. Software Used in CNC Machining
Advanced software plays a vital role in the operation of CNC machines. Programs like CAD (Computer-Aided Design) and CAM (Computer-Aided Manufacturing) facilitate the design and manufacturing processes, streamlining production and enhancing accuracy.
3. Tooling and Tool Path Optimization
Using high-quality tools and optimizing the tool path are essential for achieving the utmost precision. Factories invest in advanced tooling solutions and software algorithms to maximize efficiency and minimize wear and tear on tools.
Benefits of Using Precision CNC Machining
The benefits of adopting precision CNC machining are numerous and significant, impacting manufacturing quality and operational efficiency:
1. Enhanced Precision and Accuracy
One of the primary advantages of CNC machining is the precision it offers. With computer-controlled processes, these factories can produce parts with tolerances of just a few microns, which is critical in sectors such as aerospace and medical.
2. Cost Efficiency
While the initial investment in CNC technology can be significant, the long-term cost benefits are undeniable. By reducing waste and minimizing manual labor, manufacturers can achieve a higher return on investment over time.
3. Scalability
Precision CNC machining allows manufacturers to easily scale operations up or down based on demand. The ability to mass-produce components without compromising quality is a game-changer for many businesses.
4. Increased Flexibility
With the ability to quickly adjust machine settings, CNC machining factories can switch seamlessly between different parts and designs, allowing for greater flexibility in production schedules.
Choosing the Right Precision CNC Machining Factory
When selecting a precision CNC machining factory, several factors should be considered to ensure that you receive high-quality products:
- Experience and Reputation: Investigate the factory's experience in the industry, focusing especially on reviews and case studies.
- Technology and Equipment: Ensure the factory is equipped with the latest CNC machinery and technologies to meet your production needs.
- Certifications and Standards: Look for factories that adhere to industry standards such as ISO certifications, which can indicate their commitment to quality.
- Customer Support: Effective communication and support from the factory can significantly enhance the manufacturing experience.
Applications of Precision CNC Machining
Precision CNC machining factories cater to numerous applications across various industries:
Aerospace Industry
The aerospace sector heavily relies on CNC machining for producing components that must meet strict safety and performance standards. Parts such as engine mounts, brackets, and housings are routinely manufactured using CNC technology due to its reliability and high precision.
Automotive Industry
In the automotive world, precision CNC machining is essential for making components critical to the performance and safety of vehicles. This includes engine parts, transmission housings, and specialized tools.
Medical Devices
The medical industry uses CNC machining to produce complex instruments and devices that require exceptionally high levels of precision, such as surgical tools, implants, and diagnostic devices.
Electronics Industry
Precision machined components are vital in the electronics industry where precision is paramount for the manufacturing of casings, fittings, and circuit board housings. The demand for smaller, more complex electronic devices continues to push the boundaries of CNC technology.
Future of Precision CNC Machining
The future of precision CNC machining factories is bright as technology advances. Key trends and innovations to watch include:
1. Integration with AI and IoT
As factories embrace the Internet of Things (IoT) and Artificial Intelligence (AI), CNC machining processes will become more automated and efficient. Real-time data analysis will allow for predictive maintenance, reducing downtime.
2. Sustainable Manufacturing Practices
Environmental concerns are leading manufacturers to adopt sustainable practices. Precision CNC machining can promote waste reduction and energy efficiency, aligning with global sustainability goals.
3. Advanced Materials
With research pushing the boundaries of materials science, CNC machining will increasingly work with advanced materials such as composites and special alloys, catering to industries with specific requirements.
Conclusion
In conclusion, precision CNC machining factories are the backbone of modern manufacturing, driving efficiency, quality, and innovation. By harnessing the power of advanced technology, these factories provide essential services across various industries, from aerospace to medical devices. As manufacturing continues to evolve, the importance of CNC machining will only grow, reinforcing its status as a critical component in the quest for precision and excellence in production.
For businesses seeking superior manufacturing capabilities, understanding the intricacies of precision CNC machining can provide a competitive edge in an ever-demanding marketplace. Whether you are looking for mass production or bespoke fabrication solutions, precision CNC machining is the key to unlocking your production potential.